Workplace accidents are rarely a bolt from the blue. There are often clear signs that an organization is teetering on the brink of an accident. The purpose of this article is to help you recognize these signs and proactively safeguard your frontline workers.
According to the international labor organization (ILO), around 2.8 million workers die from occupational accidents and work-related diseases every year. And an additional 374 million suffer from non-fatal occupational accidents.
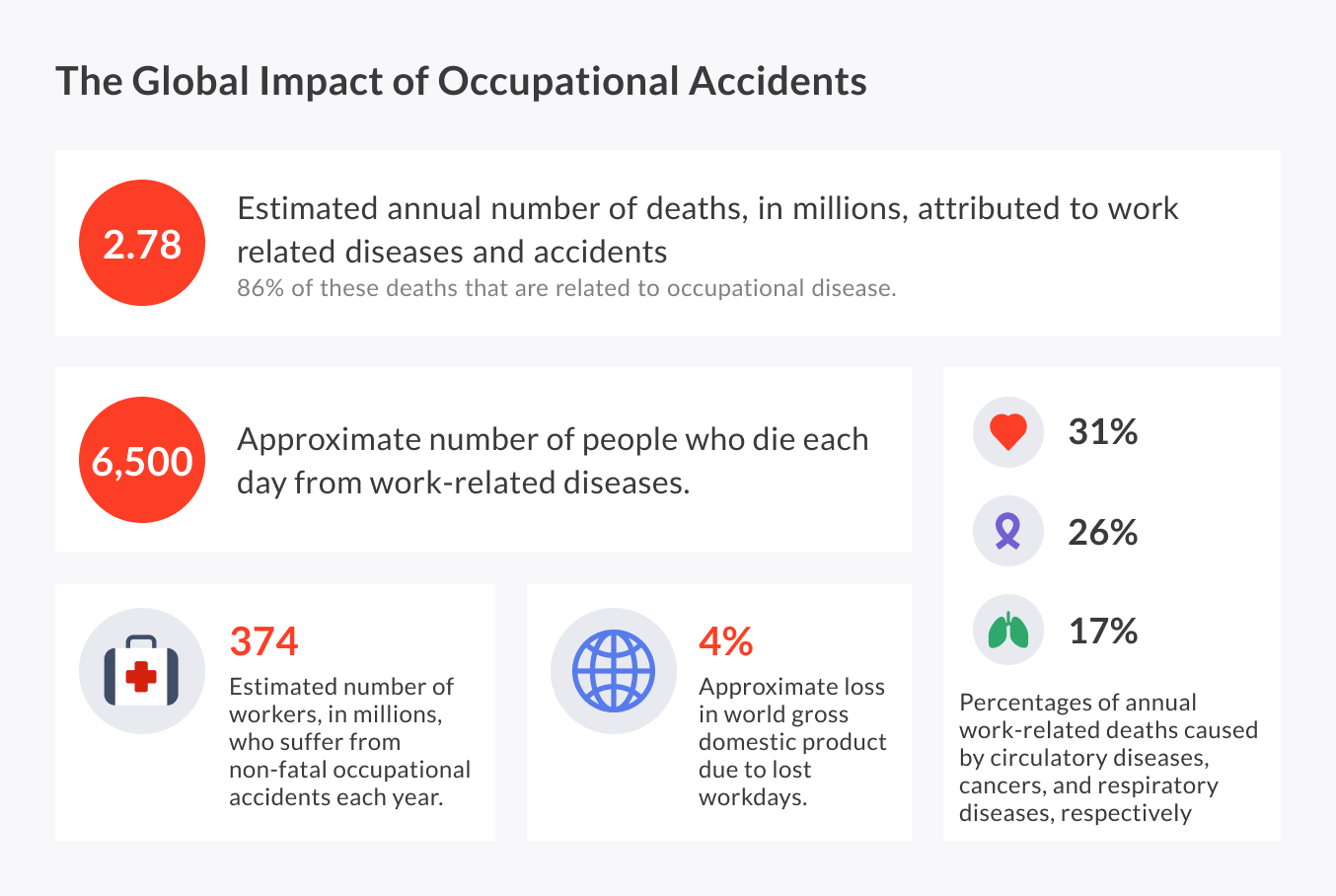
These accidents, regardless of their scale, have a cost. There is a direct cost to the victims (injury, disability, or loss of life) and an indirect cost to their family members, spouses, and dependents. Besides, as a manager or company owner, the fallout from a workplace accident may damage your company’s reputation and future prospects.
When asked what it takes to create a culture of safety, Deborah Hersman, President of the National Security Council, said “It takes listening as well as leadership. It takes data and dedication. And it takes a CEO who gets it.”
Workplace accidents are rarely a bolt from the blue. There are often clear signs that an organization is teetering on the brink of an accident. The purpose of this article is to help you recognize these signs and proactively safeguard your frontline.
So, what are some of these signs?
1. Your workers are unaware of safety protocols
Falls are the leading cause of accidents and deaths in the workplace – especially in the construction industry. OSHA placed it under the ‘Fatal Four’ incidents that caused more than half (58.6%) of construction workers’ deaths in 2018.
Also, falls are 100% preventable.
Other common accidents like electrocutions and getting struck by/caught in between objects are also preventable with safety training and protocols.
But – are you sure your workers understand and follow safety protocols? Conduct a surprise test or inspection to find out. Workers can only act out what they understand. Lengthy and boring paper guides often fail to convey information about the use of PPE, permits, and handovers – hence making these safety measures ineffective.
Digital safety guides are more interactive and can help your workers quickly grasp their role within the EHS goals of the company and be equipped with the knowledge and technical skills to perform this role.
Apart from creating interactive safety guides, you can also conduct virtual workplace training and safety certification courses for your workers. You can monitor training progress and ensure every worker completed their safety training.
2. Your field data is not digitized
Your company may produce piles of safety reports every year but linking these reports to actionable metrics may be tedious and unfeasible, especially with paper documents.
And without insight, you cannot make data-driven decisions or enable location and incident knowledge, in the case of an emergency.
Digitizing operations allows you to get real-time status updates from the frontline and ensure safety protocols are being followed.
Also, with digitized historical data, you can map out trends to better understand and resolve any safety concerns. Additionally, you can perform root-cause analysis, and know for certain which areas of the facility and worker groups have the highest risk of accidents.
3. You do not have up to date maintenance information on your machinery
Apart from falls and electrical hazards, the failure of heavy machinery and Power Industrial Vehicles are some of the major causes of accidents in a manufacturing workplace. And whilst this failure is often instigated by human decisions, it can also be caused solely by a breakdown of machinery assets.
For factories and industrial managers, having an unplanned asset breakdown is a terrifying prospect. Not only will it affect production targets and cause downtime, but it may also even result in accidents and fatalities in the workplace.
To remedy this, you should have (and execute) a pre-failure maintenance strategy for your machines.
With real-time performance data and internal sensors, you can effortlessly carry out this strategy. Also, via the captured data, you can easily measure asset performance, know their current condition, and use this information to schedule maintenance in advance of failure.
Note: Remember to isolate the machinery prior to its maintenance and use a Lock-Out, Tag-Out safety procedure.
Establishing a Proactive vs Reactive Safety Culture
Embracing a digital approach to all your operational workflows and machine maintenance is non-negotiable for the success of your company’s EHS program. But even with a digital and technological approach, accidents do happen.
And in the unfortunate event of an accident, having centralized safety protocols and emergency systems as a recovery measure will reduce the impact and consequences of the accident. Afterward, as alluded to in sign (2), you can use historical data to capture insight and learn the root causes of the accident/near misses.
You may share this information with your workers and line managers so that everyone can learn, grow, and move forward towards a safer workplace.
Have you noticed any of these signs in your facility? Or recorded a recent accident/ near miss? Learn more about our digital solutions and how they can make your workplace safer.