Every year, the ILO estimates 340 million occupational accidents worldwide. These accidents have vast-ranging humanitarian, economic, reputation, and legal consequences that make it necessary for managers to enact accident prevention strategies for their organizations. Strategies may encompass proactively identifying the root cause and combating same with appropriate corrective measures. In this article, we examine how digitalization can enhance the effectiveness and operational value of corrective measures, and produce a safer shop floor in your organization.
The four E’s of Accident Prevention
Human actions and unsafe working conditions are the major causes of accidents in the manufacturing industry. To prevent accidents from wreaking havoc in the shop floor, the onus is on managers to identify the specific root cause(s) of near-misses and swiftly correct the defects. Available corrective measures can be categorized into four groups – the 4 E’s:
- Engineering
- Education
- Enforcement
- Encouragement
Fortunately for stakeholders, the thought process and application of these measures doesn’t have to be difficult to come up with. With simple digital tools, management can turbocharge workplace safety with better, all-inclusive, and more efficient ‘corrections’ in each measure.
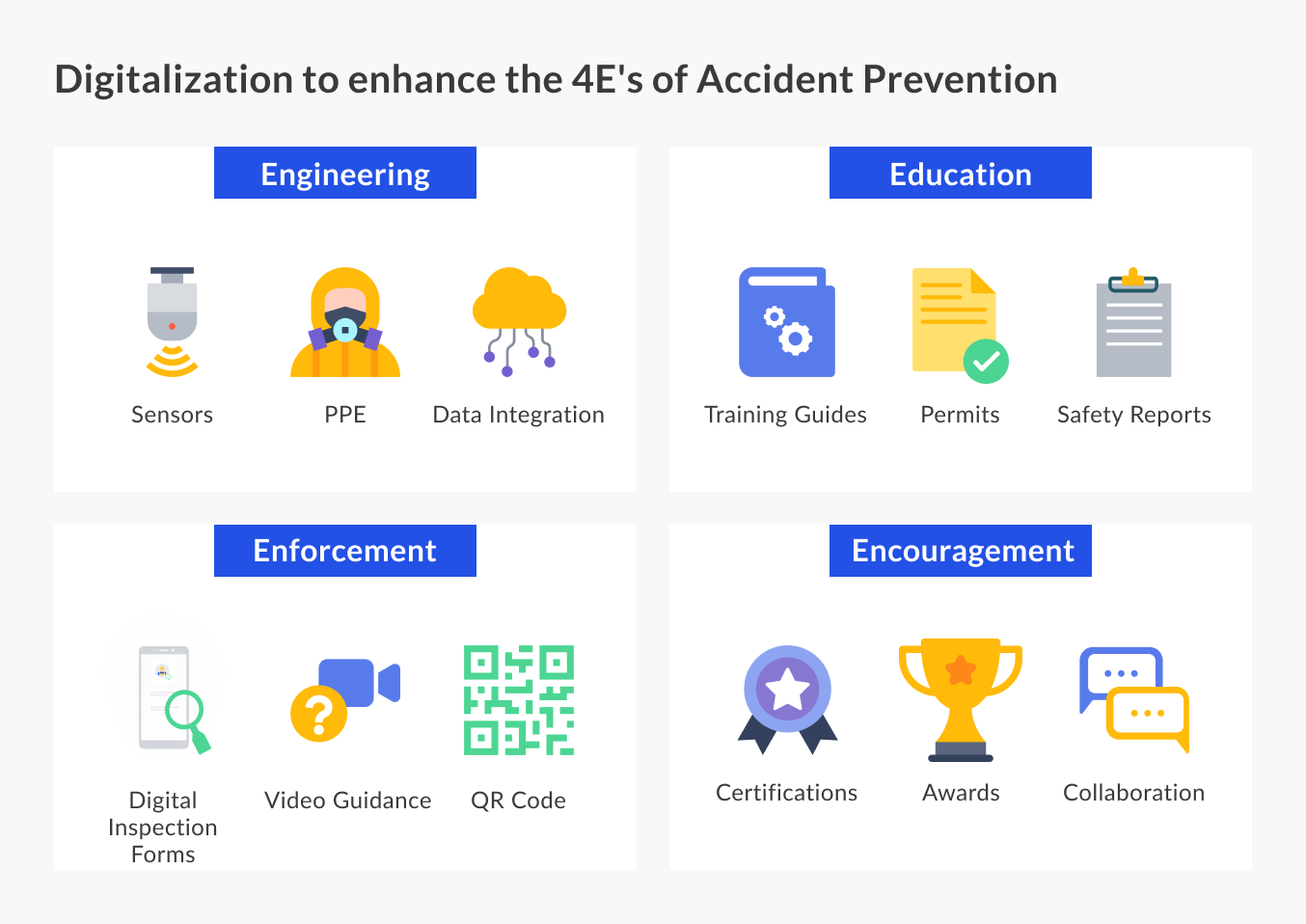
1. Engineering measures
These measures remove unsafe conditions from the work environment. Some of these conditions may be defective equipment, unguarded machinery, bad workplace design that causes mal-ventilation and congestion, excessive noise, housekeeping mishaps, and absence of PPE for workers. Sometimes, managers may not be able to eliminate these conditions entirely and will have to come up with workarounds like staggered shifts in areas where congestion is preeminent and specific PPE in areas with poor air quality or high noise levels.
Whether you are enacting corrective measures or workarounds, digitalization can be of valuable support in several ways.
Digitalization of engineering measures
- Equipment/ condition monitoring: Plant managers can attach sensors to machinery assets to track their condition prior to preventative maintenance. Such preemptive maintenance in advance of failure will limit downtime and consequently increase the factory’s efficiency and revenue.
- Data centralization: A digital platform gives workers quick access to a central database of relevant information for safety compliance. Housekeeping rosters and equipment information (historical performance, past repair dates, anticipated repair dates, operating speed, standard operating procedure, etc.) can be digitized and made available on the platform. Moreover, a digital machine guarding checklist can be provided for proper guarding and safety accountability.
2. Education measures
Human error remains the leading cause of accidents in workplaces accounting for up to 90 percent of overall incidents. Accordingly, several organizations place emphasis on regular education (training, instruction, seminars, etc.) to equip workers with the know-how and technical skills to safely perform their best work.
Here’s how digitalization can help management teams conduct better training that propels better actions by all stakeholders in their organization:
Digitalization of education measures
- Digital safety training: Digitalization provides an avenue for management to conduct sleek, visually appealing training replete with rich videos and interactive guides. During digital training, important issues like operator qualification, PPE usage, machine operating speed, and proper storage location can be addressed in an all-inclusive manner for better understanding.
- QR codes and scanners: 2D Quick response codes literally puts digital hazard information and SOP for machines at the fingertips of workers via mobile devices.
- Data-driven ergonomics: A digital platform allows managers to document safety training and contrast the data with near misses/ accident data to gauge the effectiveness of the training. Machine learning and data analysis can also be used to cull value from data so that managers can fine-tune future training in line with the needs of the organization.
Moreover, stakeholders can use historical data to analyze employee performance and better understand the ‘best fit’ from a physical, mental, and psychological perspective for worker assignment to better-suited tasks.
3. Enforcement measures:
These measures (supervision, inspections, audits, and reports) ensure safety compliance consistent with company policy and OSHA standards. Having removed unsafe conditions and actions by engineering and education measures respectively, adding enforcement measures to the accident prevention strategy enables management to maintain the new and better normal.
Digitalization of enforcement measures
- Remote inspection: Digitalization equips managers with cameras that can be positioned across the shop floor to provide live feed from remote locations. Besides fostering more collaboration, remote inspection enables project management and safety compliance monitoring, geographical barriers notwithstanding. See how Maximl enables digital inspections.
- Digital audits: Safety training, procedures, near-miss, and accident data can be stored and centralized digitally in case of audits or external inspections. Paperless and resilient storage will add more life-span to this information even as the digital solution provides a platform to conduct a systematic and thorough safety assessment. See how Maximl digitizes audit management.
- Compliance monitoring: Digitalization provides wearable technology that can be used in tandem with digital cameras to monitor worker condition and remind them of their safety responsibility in real-time.
4. Encouragement measures:
These measures boost employee morale and make them respond more positively to safety requirements on the shop floor. It includes promotion, awards, recognition, and incentives.
Workers will be more motivated and receptive to training when they see that the solutions are beneficial to their work. Moreover, they will work better when they feel valued and connected to management. Digitalization makes this possible by providing managers with a connected worker platform to effectively share valuable information like employee development programs, education opportunities, and career advice.
Maximl’s Connected Worker solution for Safety provides organizations with robust digital tools to manage the 4Es and prevent accidents in the workplace.