Manufacturers the world over use the ISO 9000 standard series to set the bar for workflows and product quality. The reality, however, is that more often than recognized, complete adherence is only on paper and may not be in full operation – implemented and enforced – across the shop floor. When this happens, disorganized workflows will occur. And further along, the quality of the factory’s products will pale in comparison to minimum standards. In this article, we observe strategies for manufacturers to sustain quality conformance and ‘get ahead of the curve’ to adequately manage non-conformance in their factories.
ISO 9001 and non-conformance
ISO 9001 is the internationally accepted standard that provides a set of stipulated guidelines for organizations to establish and follow a Quality Management System. First published in 1987, the standard is tailored after the PDCA improvement loop and is used by over a million organizations for continual process improvement and consistency of product quality. ISO 9001 helps ensure that production processes are harmonious from one country to another and aims to synchronize the quality of products available on the global market – preventing a drop-off in quality through the consumer chain. But this is not always the case.
Around the world, it’s commonplace to find manufacturers whose processes are misaligned from ISO’s 2015 update. Those who have up-to-date processes, often house stakeholders who neglect the requirements or structures ill-fitted to support the implementation of SOPs. The term non-conformance perfectly captures this situation and is used to describe a factory whose quality management system, as patterned after ISO 9001, has fallen short of established requirements.
‘In quality management, nonconformity is a deviation from a specification, a standard, or an expectation’ – Wikipedia
What happens if a factory is non-conformant?
Factories may recognize product non-conformity during routine tests or internal audits. Unfortunately, the bulk of non-conformities are identified outside the shop floor during pre-shipping quality inspections, external auditing, or more ominously, via customer complaints. The longer it takes to identify a non-conformance, the more costly it becomes to correct.
(See this post on the 1-10-100 rule).
So when a poor quality product reaches a customer, for example, the factory will have to detect the root cause of the problem and fork out extra cash for recalls, (re)production, and any litigation that may result. In addition to costly reputational damage, the factory may also have to manage fallout with the government and regulatory bodies..
Earlier detection of non-conformance, while not as serious, will still foster a hazardous working environment and lead to a decline in productivity and loss-time.
With these in mind, here are four steps to improve quality conformance and avoid the myriad of problems that non-conformance creates:
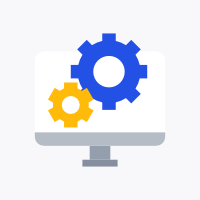
Increase accessibility to SOPs
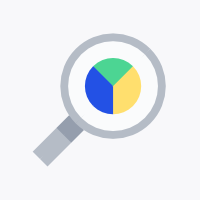
Prioritize management review and internal audits
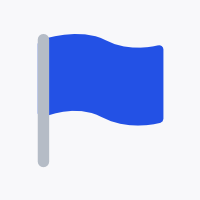
Install ‘checkpoints’ and traceability systems
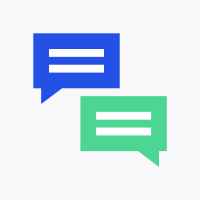
Establish clear communication channels with customers
Increase accessibility to SOPs
The two major reasons for non-conformance in quality are:
- Absence of up-to-date SOPs
- Presence of SOPs, but disregard for the procedures
The second reason is more systemic and requires a persistent culture ‘shift’ to change. The first, however, can easily be solved by providing modern SOPs for stakeholders to use. Going a step further, top management can ensure that SOPs are accessible to everyone on the shop floor. That’s why we advise employing a digitized procedure.
Unlike paper-based guides that are difficult to distribute (especially for large factories), a digitized SOP can easily be shared on the factory’s Connected Worker platform and retrieved for future reference. This allows workers, contractors, and technicians to easily access useful information for standardized and quality work. Moreover, digitizing SOPs enhances the factory’s intra-document controls, ensuring that ‘minute’ items like font size, language, etc. can easily be rendered to accommodate every stakeholder.
Prioritize management review and internal audits
Typically, organizations across broad swathes of industries regularly review their existing methods. This, for manufacturers, is very important and is a key step to ensure continued quality compliance and conformance. Reviews should be conducted as frequently as logistics and working schedules allow, but not too frequently – to create time for the conclusions from previous reviews to be implemented.
During reviews, top management in collaboration with stakeholders from each level will brainstorm issues around the factory’s working methods.
They will also address quality pain points and chart a course forward for the organization. Ideas will spring up and roles may be assigned to check the viability of suggested ideas and see to their implementation.
Furthermore, internal audits can be carried out to check the efficiency of a factory’s Quality Management System. Audits will reveal procedural failings and show what has to be done to correct (and sustain) quality conformance.
Install ‘checkpoints’ and traceability systems
A manufacturer’s production sequence should never go a cycle without quality inspections – carried out at injection terminals. If consistently executed, these inspections increase the likelihood of detecting product non-conformance during the production stage.
Also, when the result of inspections flags a product defect, it’s important that there’s a pre-installed traceability system. This is because defects will often extend more than a single product. Series of batches could be affected and some of the individual products may already be in circulation.
Traceability enables factories to effortlessly track finished products, right to the doorsteps of customers. In the event of non-conformance, the factory is positioned to issue targeted recalls and curtail the damage. Traceability can also boost in-factory quality control by equipping top management with tools to monitor individual product constituents, in real-time.
Establish clear communication channels with customers
Factories exist to satisfy the demand of customers, and they should not be aloof to their demands. Because when all systems have failed, communication – initiated by customers – is the factory’s last resort to detect a product mishap, without unwanted escalation.
Accordingly, to manage non-conformance, factories should put in place an open and manned platform to receive customer feedback. Feedback may be negative or positive, in the form of complaints or suggestions. But regardless of their nature, they can provide themes for future management reviews and fresh ideas for the quality management strategy.
Why Maximl?
Maximl helps factories to easily manage the process of implementing a track and trace solution. Our Connected Worker platform easily integrates with traceability mediums to provide a real-time measure of product quality within the factory and analyze tracking data inside and outside the factory. Moreover, we rapidly digitize ISO standards into visually appealing formats to improve accessibility, quality compliance, and conformance.
Request a demo today!
To book a demo, please visit maximl.com or, email us at hello@maximl.com
Download content

This content is locked
Please enter the following details to unlock the content