Maximl and DuPont Sustainable Solutions deliver digital transformation throughout safety operations to help Chemical giant save countless hours wasted on processing paper towers and protecting their workplace with digitally enhanced safety compliance.
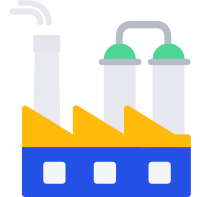
Client
European
Chemical giant
Presence in
Europe across
15+ sites
1000+ Users
Key Results
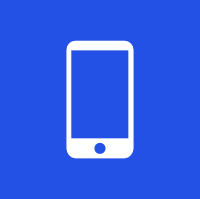
Replacing paper processes with a digital approach resulted in standardization of key processes across all sites, improved user experience and created reliable digital solutions for 1000+ users.
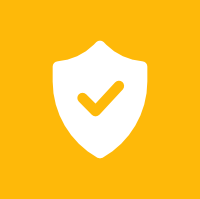
Undertaking a digital approach decreased safety-related hazards and helped the company shift to a proactive safety culture.
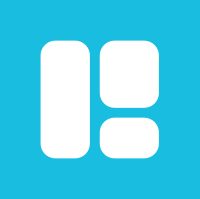
Management had more visibility into operation with centralized module to correctly track and prioritize tasks with access to real-time digital data. The availability of persona-based dashboards allowed for more advanced planning and strategizing for the future.
Challenge
The organization’s existing paper-based procedures made it difficult to achieve their goal of complete standardization to reduce the risks associated with their safety operations. Because of its reliance on paper-based procedures, the organization was unable to establish and implement EHS processes such as Preventive Safety Observations, Safety Inspections, Permit to Work Audit, and Verification of Safe Work.
Problem
Especially for a chemical manufacturing company, the nature of the hazards involved are grave. Hence, the inability to implement and track safety measures correctly required urgent attention. Employees place themselves at risk directly if they do not comprehend and follow safety procedures but they are also put at danger if the organization is unable to trace mistakes, whether behavioural or documentational in character to proactively prevent similar accidents .
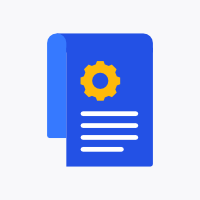
Employees were unaware of safety-related information because it was challenging to keep up with paper-based procedures
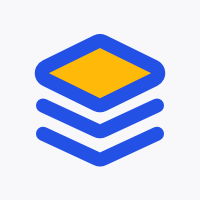
Due to the numerous paper-based processes that needed to be handled, managers struggled to maintain a methodical approach to fostering a safety culture
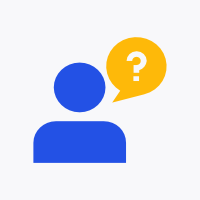
Employees were unaware of the safety procedures' functionality, as well as the value of a safe culture, and how it benefits them directly
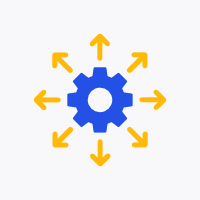
Due to the lack of a centralized system, the organization struggled to prioritize tasks and execute them across the various sites
Solutions
Along with our partner, DSS, we designed and deployed digital solutions on Maximl’s Connected Worker platform to enhance safety measures in the last-mile and drive adoption among all stakeholders.
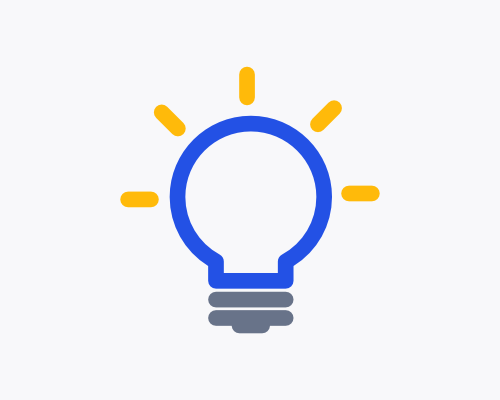
Understanding Users and Use-Cases
Our team worked closely with management to understand the existing safety culture, the most common issues, and the various stakeholder points of view across all the sites.
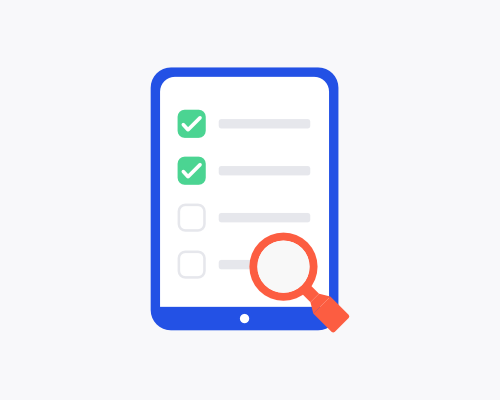
No Code Solutions
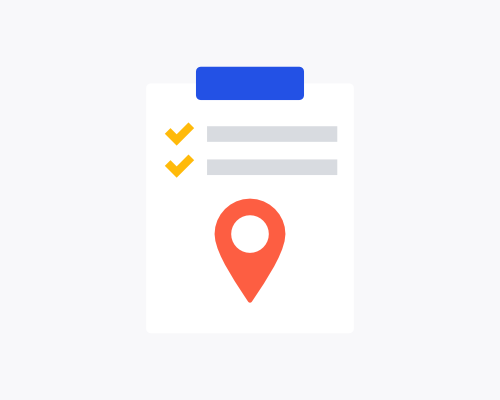
Action Assignment & Tracking
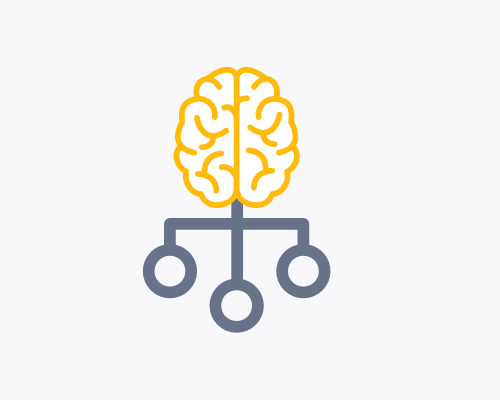
Centralized Knowledge Base
About Maximl
Maximl’s Connected Worker platform is built to drive adoption among deskless workers and enable Standard Work Implementation on the field. Our low code platform hosts a powerful suite of mobile-first solutions that are customization-friendly and scalable.
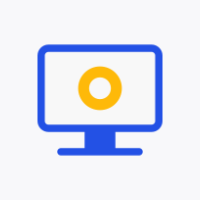
Digitize hundreds of rigid paper-based SOPs and covert them into interactive work instructions that can be deployed within weeks.
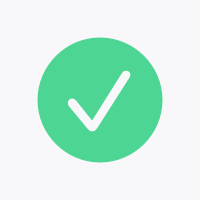
Trigger corrective actions based on deviations recorded in key metrics.
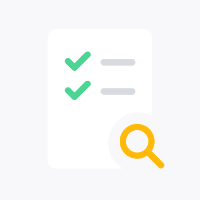
Conduct digital inspections across the value chain- from industrial assets, workshops, warehouses, to contract partner locations.
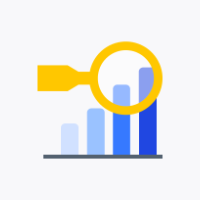
Leverage rich analytics to continuously enhance workforce performance with digital implementation of Kaizen, Six Sigma and Lean initiatives.
Request a demo today!
To book a demo, please visit maximl.com or, email us at hello@maximl.com
Download content

This content is locked
Please enter the following details to unlock the content