Every so often, factories conduct quality inspections to detect manufacturing defects during different stages of supply chain. This is to ensure that their products follow evaluation sequences that guarantee impeccable quality for their customers. Sequel to a product failing these inspections, the factory will normally take measures – preventive, corrective, and failure – to ensure that the quality is upheld and maintained. In this article, we examine how factories can strategize off the 1-10-100 rule and benefit from prioritizing early detections of defects in the supply chain. This helps keep the appraisal costs in check. We also look at how a Connected Worker platform is the ideal solution to help implement this task.
The manufacturing conundrum: Appraisal Costs vs Profit
It’s commonplace in Industry to limit the scope of pre-production inspections or stop it altogether. Many factories do this to avoid appraisal costs – which can be significant and may sometimes involve third-party companies. The result of this is that factories may not capture defects during sourcing and will become liable to costly interventions down the line.
An ounce of prevention is worth a pound of cure – Benjamin Franklin
As we’ll soon examine from the 1-10-100 rule, cutting appraisal costs to increase profit margins is massively short-sighted. The far-ranging cost of discovering poor quality late in the supply chain magnifies the cost of production in the short term and can start a chain of events that puts the factory out of business in the long term.
What’s the 1-10-100 rule?
Applied to manufacturing’s supply chain, the 1-10-100 rule states that cost increases by a factor of 10 if a quality issue is undetected in each stage of the chain.
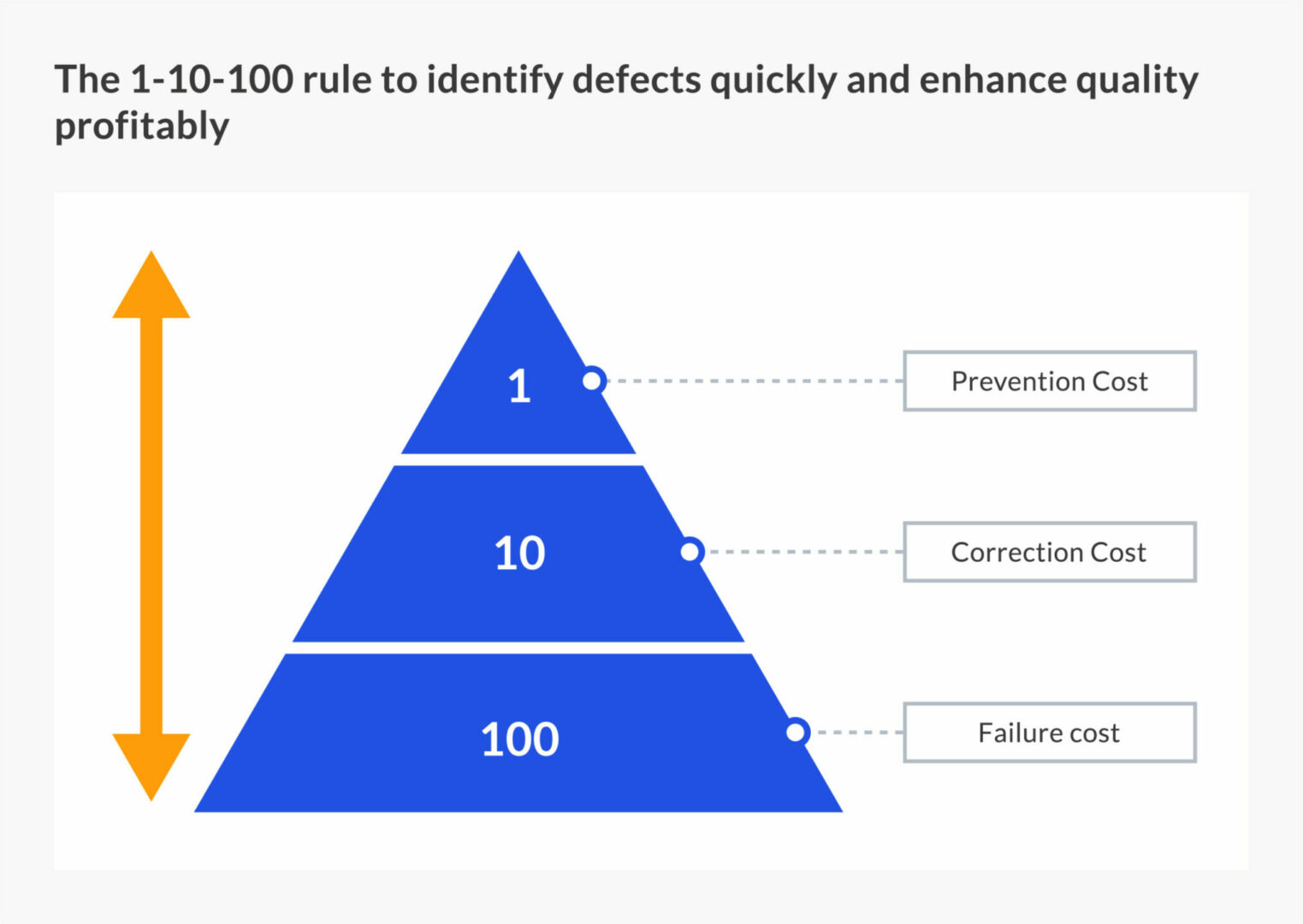
That is, if it costs $1 to detect (and solve) a product defect pre-production, it will cost $10 to do so during production and if the problem is still unresolved, $100 will be forked out post-production.
The 1, 10, and the 100: How discovering defects affect manufacturing at each stage of the supply chain
The 1: Pre-production
Before production, the bulk of manufacturing work is centered on product development and inspections of raw materials. Finding a flaw with the product design has very little forbearing on the factory’s finances as they can simply correct the schematics or collaborate with an expert designer. Moving forward, if defects are detected in raw materials, the factory may only incur delay to production as the cost and liability of reordering inventory should veer towards the supplier.
So overall, the cost of early detection is minute and has little bearings on revenue. On the upside, if rigorous early inspections are passed, the factory can ramp up productivity with quality and production-ready raw materials.
The 10: Production
The actual cost of detecting a defect during production depends on the stage of detection. At the start of production, the factory, having accepted and (in legal terms) deemed the raw materials satisfactory, may have to bear the financial and logistics brunt of reordering inventory.
At the latter stages of production, a defect will cost the factory corrective and preventive costs. The former is the cost of fixing the product defect and includes conducting root cause analysis, reworking, or reproducing new products. And the latter is the cost of putting systems and measures in place to reduce the likelihood of a similar occurrence in the future.
In addition to these costs, the factory will also have wasted resource input and may no longer be able to meet up with already established orders which can unsettle customers.
And the 100: post-production
The unfortunate and avoidable event of a failed pre-shipment inspection can quickly plunge the factory into ‘scramble’ mode. First, they will need to find the root cause of the problems, which depending on available internal traceability measures, may be expensive and time-consuming. Then, they will need to rework defects or discard already produced goods. This is besides the preventive costs, extra overhead, and valuable time the factory expends.
Defects may also be discovered further along when the product is already in circulation. In this case, the factory will be left in an unenviable position of issuing recalls (and shouldering warranty and other associated costs), navigating litigation, and soliciting PR to ‘control’ the resulting narrative. If the products have caused injury, harm, or loss of life to customers, the damage to the factory may be irreversible. Information passes around very quickly nowadays and within a short period of time, the general public and competitors will get wind of the situation and react accordingly.
6 ways a Connected Worker solution improves product quality and inspection
- Digitized SOPs and Standards
- Audits
- Monitor qualifications
- Complaint handling
- Integrate, centralize and store supply chain data
- Quick communication
Digitized SOPs and Standards
Digitized SOPs and paper-based standards remove barriers to accessibility and increase worker assimilation to standards. When guides are digitized and made available on a platform, workers will no longer be limited by unavailable or bulky leaves, and are more likely to consult the set-out production processes and quality control. Moreover, they can easily refer to the guides for FAQs concerning quality compliance and view up-to-date information on how best to react when a defect is flagged during production.
Audits
A Connected Worker platform simplifies the task of policing compliance. Through digital displays and audits, managers can remotely monitor the work environment and have real-time visual oversight of production processes. They can access digital production records, and depending on the sophistication of traceability, may be able to confirm the components of individual products at every stage of the production process.
Monitor qualifications
Using a connected worker platform, factories can monitor the qualifications of internal pre-production inspectors and in-factory workers to ensure that they have the requisite (and up-to-date) training, and licenses to inspect raw materials and detect flaws.
Complaint handling
A platform solution provides a simple and convenient way for the factory to handle complaints – by allowing customers to remotely fill out product problems using a digital form. The customers can provide an image of the product defect or send in videos showing the adverse effects of using the products. With a dedicated staff in place to receive these complaints, the factory’s top management will be promptly notified of product mishaps and can respond quickly to minimize the cost of failure.
Integrate, centralize, and store supply chain data
Data on suppliers, partners, and customers can be centralized and safeguarded on a digital platform. This way, the factory can easily analyze trends, categorize information, and will not be subject to paper-based files that can easily be destroyed or misplaced. Moreover, the factory can reduce the time lag for searching up relevant information and shorten its response time to product recalls.
Quick communication
Updated SOPs and important regulatory briefs can be swiftly disseminated across the shop floor to fast-track implementation. Also, managers can remotely collaborate with inspectors to ensure that raw materials are subjected to rigorous checks and screening. And if a product defect is discovered, this information can be passed across to stakeholders in real-time to limit escalation.
Why Maximl?
Maximl’s low-code Connected Worker platform has helped leading factories streamline safety, quality, and maintenance procedures on their shop floor. Our solution requires little onboarding, integrates with enterprise-wide systems, and provides a holistic view of end-to-end factory assets.
Maximl Features
- Digitizes quality standards and procedures in a few minutes
- Enriches communication and collaboration
- Supports multimedia attachment for complaints
- Works offline in low-connectivity areas