Good, usable work instructions are a vital aspect of a manufacturing work. Apart from improving safety and operational efficiency, instructions secure knowledge from legacy workers for process continuity, when these workers/operators eventually retire. However, for work instructions to be effective, they must be consistent with the realities of the shop floor and properly formatted for easy assimilation and quick follow-through. In this article, we examine off-document and on-document strategies to create engaging and interactive digital work instructions for your manufacturing unit.
Before the emergence and widespread use of digitization tools, paper instructions were the only option for many manufacturing setups. But paper, besides the cost of production, was difficult to keep track of and easily susceptible to damage. And in most cases, the logistics of disseminating paper to several operators at far distances proved insurmountable.
Now thanks to the advent of rapid digitization, these difficulties are a thing of the past. Right from a leading Connected Worker platform such as Maximl, slick and visually-rich standardized work instructions can be created and effectively shared to operators, far and wide. More cost-effective, the digitized work instructions can be resiliently stored for future reference and translated into multiple languages to overcome geographical silos.
But despite the obvious operational value, merely digitizing work instructions does not guarantee its effectiveness. Like paper, these may lack clarity and precision, and be inefficient in their single purpose – describing the correct way to perform a task. The digital document, however slick, may not successfully convey the standardized work instructions and may yet be ignored by operators.
5 steps to build great digital work instructions (Template):
The steps provided below helps create digital work instructions that operator adhere to:
- Understand the process: understand your workers
- On document: Follow a consistent structure
- On document: Break up text with visuals
- Standardize and enforce
- Learn from feedback
1. Understand the process: Understand your workers
To build interactive work instructions that resonate with operators, you need to have a working understanding of the processes and peculiarities of the factory floor. You may gain this understanding from direct, first-hand experience i.e. devoting time to observe the shop floor and undertaking relevant shop floor training or indirect experience i.e. gaining insight from those who’ve spent significant time on the shop floor or have undergone said training. Experience – obtained directly or indirectly – will enhance your credibility as an instruction author which in turn will lead to greater compliance with the created instructions.
Also important is the need to understand your operators: their mindset, shop-floor expertise, and digital fluency. Have the operators undergone training and do they have the skills to carry out tasks in the established order? Do they see work instructions as vital to every task? If so, is there an overall positive view on digitized work instructions? Moreover, are operators adept in digital usage, or will additional training be required to acquaint them with digital instructions?
The answers to these questions will help you normalize digital work instructions and enhance their effectiveness.
2. On document: Follow a consistent structure
Whether or not a work instruction is effective and serves the end goal for which it was intended will depend to a large extent on the organizational structure of the document.
Shop floor workers are busy people, most of who work in physically exertive roles. When they use digital work instructions, they expect that these instructions are visual and organized in such a way that it’s easy-to-understand, saves time, and requires little mental exertion. Upon a long day’s work, having to make sense of disorganized work instructions or SOPs may be demoralizing for some – a state of mind that will likely lead to non-compliance with standards.
Without fail, digitized SOPs should possess a consistency of structure that forefronts the most important information, relevant to the operator for that particular task. It should be user-centric – with work instructions presented from the operator vantage point, bear large fonts (in cases of vision problems), and ideally, written out in a bulleted or numbered list.
Some key elements in a structured SOP include:
- Title of work instruction
- Author of work instruction (required: insert factory title or qualifications)
- The objective of the work instruction
- Purpose of the particular task
- Tools required to perform the task
- A step-by-step guide to performing the task
- The expected result of performing the task
- Interactive visual elements interspersed in the work instructions
- Safety tips, warnings, and associated risks (preferably embedded via information mapping underneath to avoid information overload)
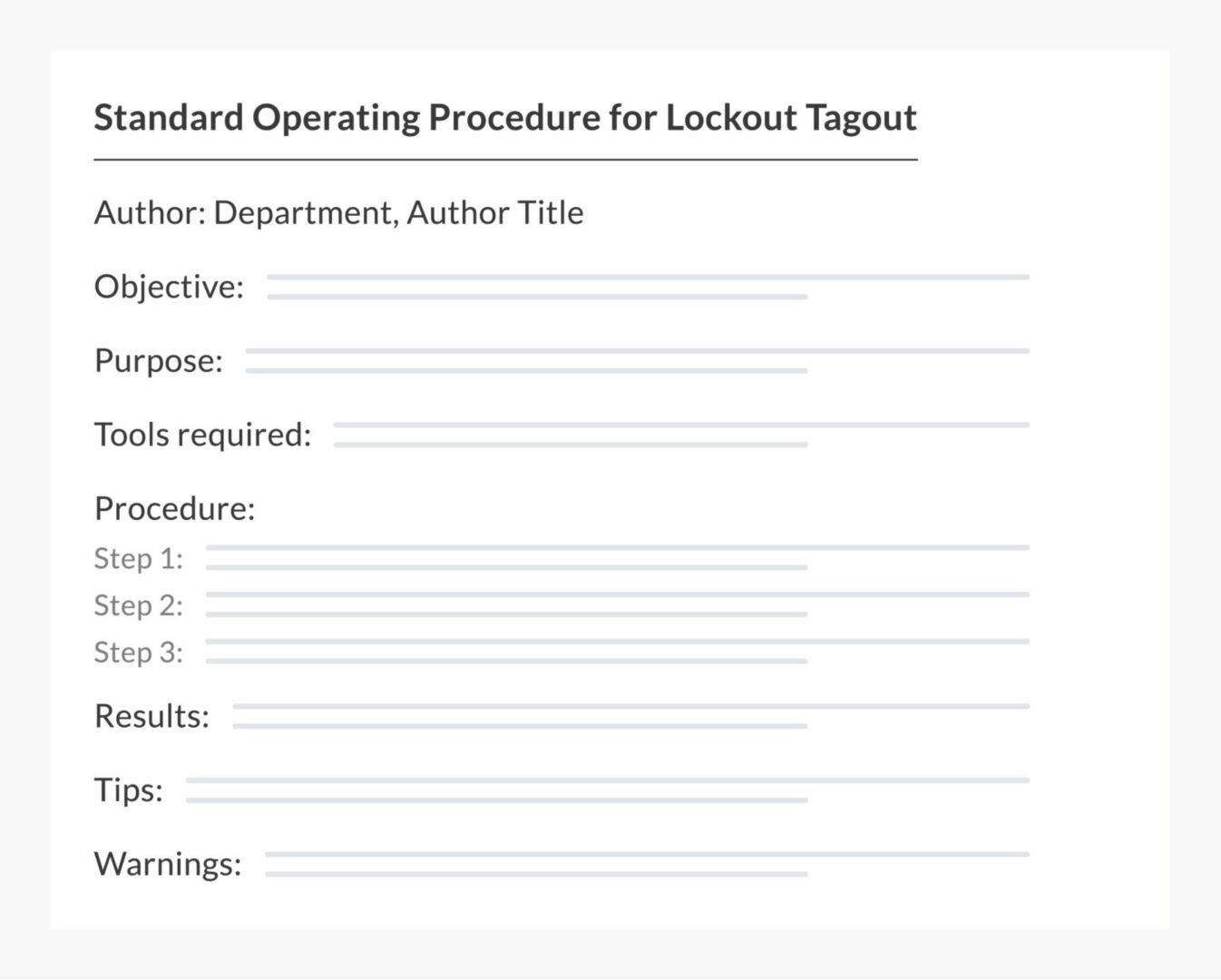
3. On document: Break up text with visuals
90% of the information processed by the brain is visual.
As an action-oriented space, the manufacturing industry merits action-based depictions of work instructions. While text will work in some cases, the best way to convey action is through interactive and visual work instructions that leave the operator in no doubt as to the correct way to perform a task. Besides, presenting work instructions in lengthy text, digitized or not, will very likely result in a mental mix-up, especially in a tired mind.
Good work instructions are always presented digitally and interspersed with visual ‘breaks’. The text snippets are rendered in a clear, objective, and concise language with jargon and industry-specific terms used only when necessary. Also, sentences are straight-to-the-point and action-based (preferably containing single verb actions for each sub-task).
To supercharge the effect of the message, the documents are sprinkled with multimedia attachments like images, graphic illustrations, hyperlinks, audio recordings, video, and animated walk-throughs. The overall instruction is minimalist in design with white space used to enhance readability.
4. Standardize and enforce
There’s no point building digital work instructions if it’s inaccessible to shop floor operators or ignored during work processes. In other words, building an impressive instruction is not enough – usage must be enforced and its importance repeatedly communicated to operators on the shop floor. On-boarding and training programs provide a unique opportunity in this regard. You can trump up the value of your standardized work instructions and remind workers that no matter how familiar they are with a process, these should remain an essential part of their work.
To improve the accessibility of digital instructions, the easiest and most convenient way is through a Connected Worker platform. On the platform, already existing work instructions can be rapidly digitized and new standardized work instructions beautifully designed from scratch. More relatedly, these instructions can be shared to the mobile devices of every operator, and expertly managed to ensure operators have access to an archive of digitized work instructions for reference and knowledge-building.
Operators, on the other hand, can use their dashboard to collaborate on instructions, offer input and provide feedback.
5. Learn from feedback
No work instruction; digital or not, is perfect. There may be flaws, gaps, and lapses that only a fresh perspective can spot. Whereas you may consider it spot-on, an operator may see the text as indecipherable or the visuals as unclear. Even yet, operators may be locked out of the document altogether.
Feedback – enabled on a Connected Worker platform – allows you to implement swift corrections, improve the organization (and permission management) of the document, and ‘error-proof’ future work instructions.