Production’s primary aim should be to ensure that, without fail, every unit of output meets the minimum safety standards and at no time endangers public health. But straightforward as it seems, this aim is not always met. Burdened by pre-production errors, cumbersome workflows, and unstandardized procedures, many factories occasionally (and routinely) fall short of good manufacturing practices. In this article, we examine these practices and outline 9 all-encompassing principles of good manufacturing practice that every factory should follow.
Good Manufacturing Practice (GMP)
The concept of product safety has evolved to good effect over the decades. Far removed are we from the 20th century where tragic events, related to abysmal product quality and often having fatal consequences, was a fixture in newspapers. These events did serve to trigger an increased emphasis on health and safety, leading to the normalization (at least in principle) of good manufacturing practices around the World.
“Good manufacturing practice (GMP) is that part of quality assurance {that} ensures that products are consistently produced and controlled to the quality standards appropriate to their intended use and as required by the marketing authorization.” – WHO
First formulated by the World Health Organization in 1975, the term ‘Good Manufacturing Practice’ describes a set of recommendations for production processes – consistent with quality standards and executed in such a way that output is safe and healthy. Good Manufacturing Practice begins from the pre-production planning stage and carries on through to sourcing, and actual production up until shipping.
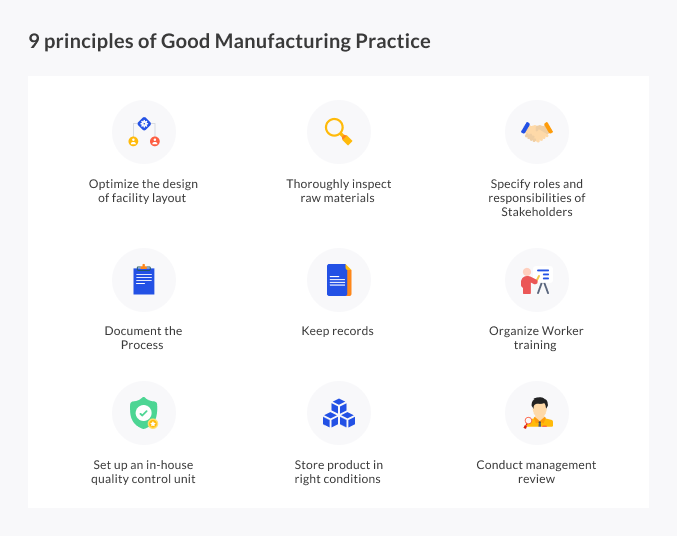
Optimize the design of facility layout
The location, design, and overall ambiance of a production facility are key elements that should be considered before manufacturing commences. Putting forethought into these elements will reduce the likelihood of hazardous occurrence and contamination of product constituents during production. Also important is to plan a linear production sequence and consider the suitability of environmental variables (air, temperature, and humidity) to the intended product.
Moreover, ergonomic considerations like factory lighting, sitting configuration, and equipment fit-to-work should be thoroughly controlled. This will provide ‘that extra 10%’ and add genuine value to productivity and efficiency in the plant.
Thoroughly inspect raw materials
This is a crucial and oft-ignored step in good manufacturing practice. When raw materials are thoroughly inspected, a factory can notice defects and illicit swaps at the outset. Inspections may involve checking for exterior material damage or testing several samples at random. Getting these inspections right will reduce the likelihood of damaging production mishaps and more costly corrective actions at a later stage.
Specify roles and responsibilities of Stakeholders
Good, harmonious manufacturing requires that roles and responsibilities be clearly defined and communicated. No ambiguity should exist in job descriptions, shift changeovers, and task schedules. From top to bottom of the plant, everyone should know their individual schedules and have a documented material – paper-written or preferably digital – to consult in case of last-minute changes.
Document the Process
One of the objectives of Good Manufacturing Practice is consistency. Essentially, this means that the process, set on ‘auto-repeat’, should yield products of standard quality, every single time. This is where Standard Operating Procedures (SOPs) come in.
SOPs render the work procedure sequentially and orderly so that workers without prior experience can follow these procedures and still achieve the same results as a legacy worker would. For best results, SOPs should be written with minimal jargon and have visual cues that will make them easy to understand and follow. For even better results, the SOPs should be easy to access via smartphones and devices á la digital age.
Keep records
Records may be about personnel (see principle 3), machine assets, or supply chain stakeholders – upstream and downstream. Regardless of their nature, all records must be stored and preserved. In addition to face value, record-keeping is useful for project management and can serve as a basis for strategy and decision-making.
Cloud platforms provide more storage resilience as opposed to paper records that can easily be lost and destroyed.
Organize Employee Training
Worker training and refresher courses – regularly conducted – is a non-negotiable aspect of Good Manufacturing Practices. Training should not merely be confined to job tasks but should also delve into areas like workplace hygiene, working models, and emerging technologies. Furthermore, in keeping with the construction and manufacturing industry, training should be hands-on so that actual skill transfer can occur.
Set up an in-house quality control unit
A quality control unit is an independent unit within the factory that takes up the responsibility of running tests on the processes and the products. They supervise the operations, validate the processes and ensure that SOPs are followed during the production sequence. This unit is an important feature for factories, not least in the area of impromptu external inspections.
Store product in right conditions
Sometimes, the entire process from the raw materials to the final product follows Standard Operating Procedures, but the good work is undermined by unsuitable storage facilities. The finished product, whether remaining in-factory or en route to delivery, should be kept at optimum conditions, in an area devoid of contaminants.
Conduct management review
Reviews are the ‘seal’ of Good Manufacturing Practice and set the factory on course for continual improvements. They should be conducted by the factory’s top management, in collaboration with stakeholders, up and down the supply chain. Together under the same ‘roof’, reviews allow everyone to grasp the bigger picture, discuss problems and proffer solutions for growth.
Why Maximl?
Maximl’s Connected Worker platform provides a medium for factories to digitally document their processes, in line with industry 4.0. Our platform is cloud-enabled so that these documents, along with other asset/ production records, can be resiliently stored.