One of the foremost desires of businesses around the world is to relentlessly drive improvement in their processes and products. While concepts to fulfill this desire may differ, the approaches are often rooted in PDCA. Also known as the Deming wheel or Shewhart cycle, PDCA (plan, do, check, act) is an experimentation-based process where repetitive iterations are used for the purpose of improvement. In this article, we analyze the importance of PDCA for factories and study the role of a Connected Worker solution in creating easier and more manageable PDCAs.
PDCA for manufacturing
Processes deemed to be inadequate in manufacturing can be subjected to the ‘PDCA feedback loop’. This means that each PDCA cycle provides mining data for the next. This approach enables continual process improvement as the results of the PDCA can be used to facilitate agile manufacturing where sub-standard processes are regularly enhanced and working processes are improved to ‘near perfection’.
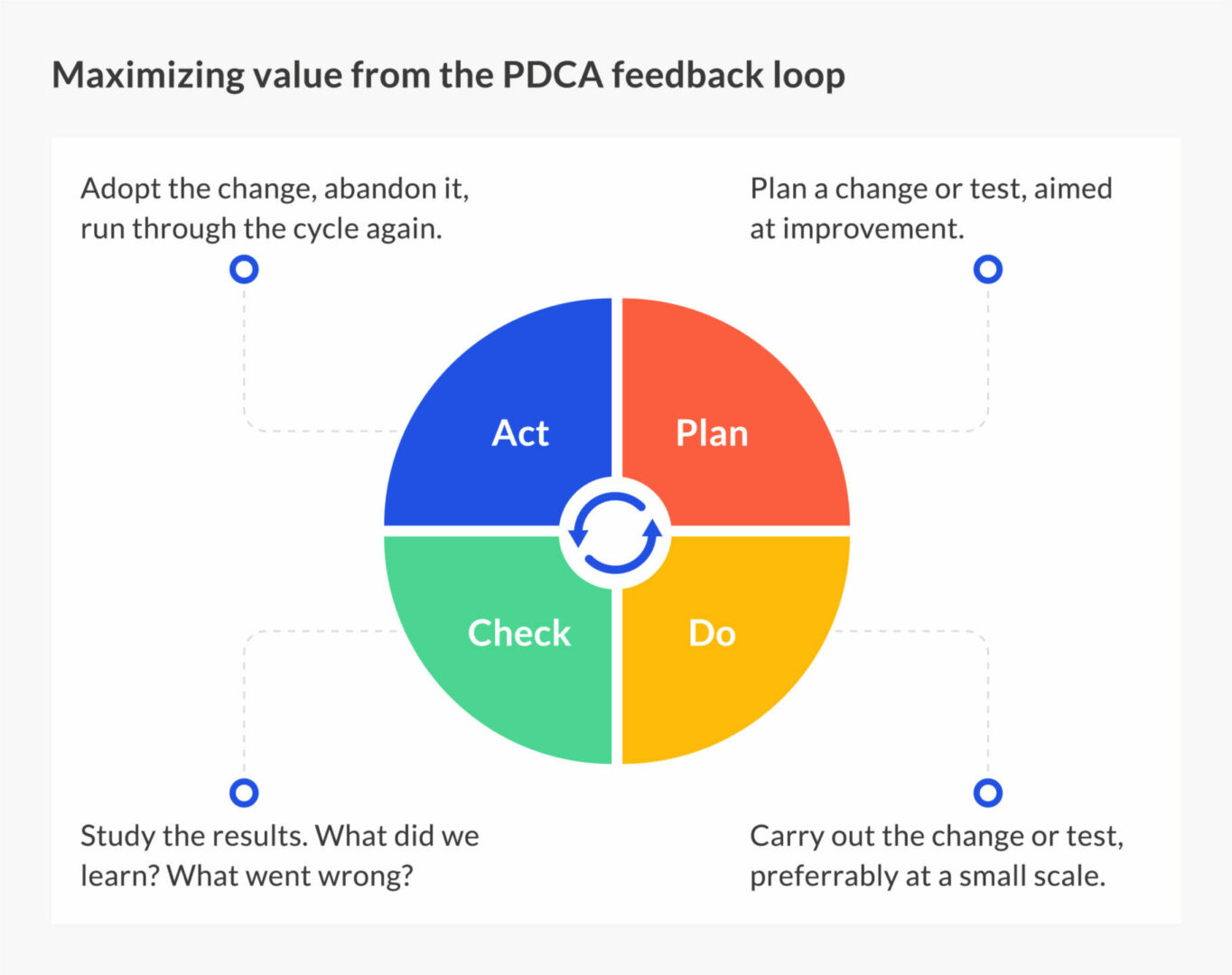
Plan
The planning phase is where a factory identifies a problem or a lagging process and devises means for improvement. First, the factory seeks to understand the scope of the problem and deduce some of the underlying causes. During this process, managers may have ‘normal’ conversations with workers most affected by the problem and collaborate with key stakeholders to spark up ideas about some possible solutions.
Afterward, the factory can appraise the solutions, pick the one with the highest potential and formulate SMART (specific, measurable, attainable, relevant, and timely) goals from which to measure success or failure. The factory can also quantitatively measure the state of the current process using surveys. This will provide a point-of-reference during the ‘check’ phase.
Do
At this phase, an expected solution is tested out – in an environment that mirrors the realities of the factory floor but on a limited scope. Doing this will reduce waste and minimize the risk to the business while still providing data to check the implementation-worthiness of the potential solution. This phase can be repeated in several pilot stages i.e., tested out in another department or geographical area to validate the results.
Check
Working off the SMART goals and quantitative results from the ‘plan’ phase, the factory can now compare the results of the solution to the pre-established KPIs. Depending on the results, they may restart with another solution from the ‘plan’ phase, modify and rerun the ‘do’ phase or move on to the action phase.
Act
When the targeted solution in phase (1) has gone through phases (2) and (3) – demonstrating acceptable results, then the solution can be implemented to replace the previous process. Any future PDCAs will use this solution as the new benchmark for improving the process.
To continue the chain of process improvement, the factory can collect quantitative feedback from workers or stakeholders after implementation. This quantitative feedback will serve as the base KPI for future PDCAs.
Why do factories need PDCA?
The PDCA tool can be used to improve manufacturing’s processes across the supply chain.
- Pre-production (planning + sourcing), PDCA enhances product development and improves the quality of raw materials.
- During production, areas like resource management, project management, and product quality can be improved under the lens of PDCA. The factory can also improve processes concerning its safety, quality, and maintenance operations.
- Moving forward, PDCA can be used to remedy slow product delivery and expertly manage the factory’s foray into emerging processes i.e. digital transformation.
The role of a Connected Worker platform in maximizing value from PDCA
- Streamlines PDCA
- Provides real-time visibility
- Enhances quality of training for implementation
- Stores results
1. Streamlines PDCA
A Connected Worker platform enables factories to obtain significant value from PDCA. The improvement process: from start to finish, from one use case to another, becomes easy to manage. The factory can customize its process dashboard to suit the unique scenario and KPIs, and set alerts to trigger when key performance metrics are exceeded. The color variations on the platform should provide visually appealing results while built-in statistic tools can help the factory to better quantify the success of the PDCA.
2. Provides real-time visibility
During PDCAs, changes are often deployed, especially between the ‘do’ and ‘check’ phases. Manually keeping track of these changes is tedious, time-consuming, and with the availability of platform solutions, unnecessary. A Connected Worker platform provides real-time visibility into the changes via a history tab. Managers can use this feature to bring out potential solutions that may have previously been discarded.
Besides real-time visibility, the digital deployment of PDCAs enhances the capabilities of factories to quickly analyze solutions and spot trends.
3. Enhances quality of training for implementation
As most organizations will second, there’s a difference between pilot-testing a solution and actually implementing it on an enterprise-wide scale – not least, in the aspect of training. For example, when factories undergo digital transformation, they have to account for (and remedy) the low digital fluency across their workforce. The factory has to teach its workers how to use digital tools and what digital working models require. And this has to be achieved in a manner that isn’t mentally exertive so that it doesn’t adversely affect their current tasks.
Digital deployment simplifies training during the ‘act’ phase with easy-to-understand, visually rich guides that help workers quickly grasp their role in a new solution. For last-mile workers, they can benefit from remote learning and will have tools to stay in communication with their managers to ensure PDCA alignment.
4. Store results
PDCA, while simple, remains a slow and long-term approach to improving a process. Each loop, with all the alterations and changes, provides a data trail from which the factory can gain insight. However, without proper storage, valuable elements of the process will be lost and the factory will have failed to fully harness the capabilities of PDCA.
A Connected Worker platform provides a medium for the factory to resiliently store data from every single loop of the PDCA. The historical data amassed over time can be thoroughly analyzed using machine learning or artificial intelligence to observe new patterns and gain additional value.
Why Maximl?
Maximl’s Connected Worker platform helps factories define, measure, and track their PDCA quantifiers. Our platform is fitted to solve hundreds of use-cases to save time and reduce the learning curve for last-mile workers. Maximlis easy-to-use, fully customizable, and supports fishbone and affinity diagrams for better PDCA analysis.