The 21st-century manufacturing industry is a truly global space with complex and in most cases, far-ranging supply chains. Raw materials may be sourced from one continent, manufacturing proper may take place in another and the distributors may be across the Atlantic in yet another continent. With such intricate parts covering thousands or millions of ‘active’ products in a global ecosystem, having the ability to know product origin and destination (right down to constituent parts for machines) is absolutely crucial. In this article, we examine why your manufacturing company needs a track and trace solution and what you should look for when implementing a solution.
What is track and trace?
According to ISO 8402:1994, traceability (comprising track and trace) is defined as ‘the ability to trace the history, application or location of an entity by means of recorded identifications’. It is the process of applying permanent or non-permanent markings on raw materials, product parts, or finished product package to monitor a product’s journey from pre-production to eventual usage. “To deliver value across the entire supply chain, full track and trace needs to be established, and transparency of the transactions need to be guaranteed,” – Dr Jyrki Syvaeri, head of global process management operations, Boehringer Ingelheim.
A key feature in quality control, track and trace typically provide information on the product life cycle, and inspection notes associated with a product.
How do you track and trace?
Track and trace can be accomplished with serial numbers assigned at the individual product level, production lots, or batches. Ideally, product markings at all three tiers should be permanently rendered. Through lasers, 2D barcodes or pin marking technology, permanent inscriptions that will withstand the usual grind and wear of manufacturing’s supply chain can be etched on a product.
For effective data management, the serial numbers system should be integrated with a digital platform where it can be catalogued and aggregated. The alternative, manually inputting on paper is tedious and susceptible to damage.
Types of traceability
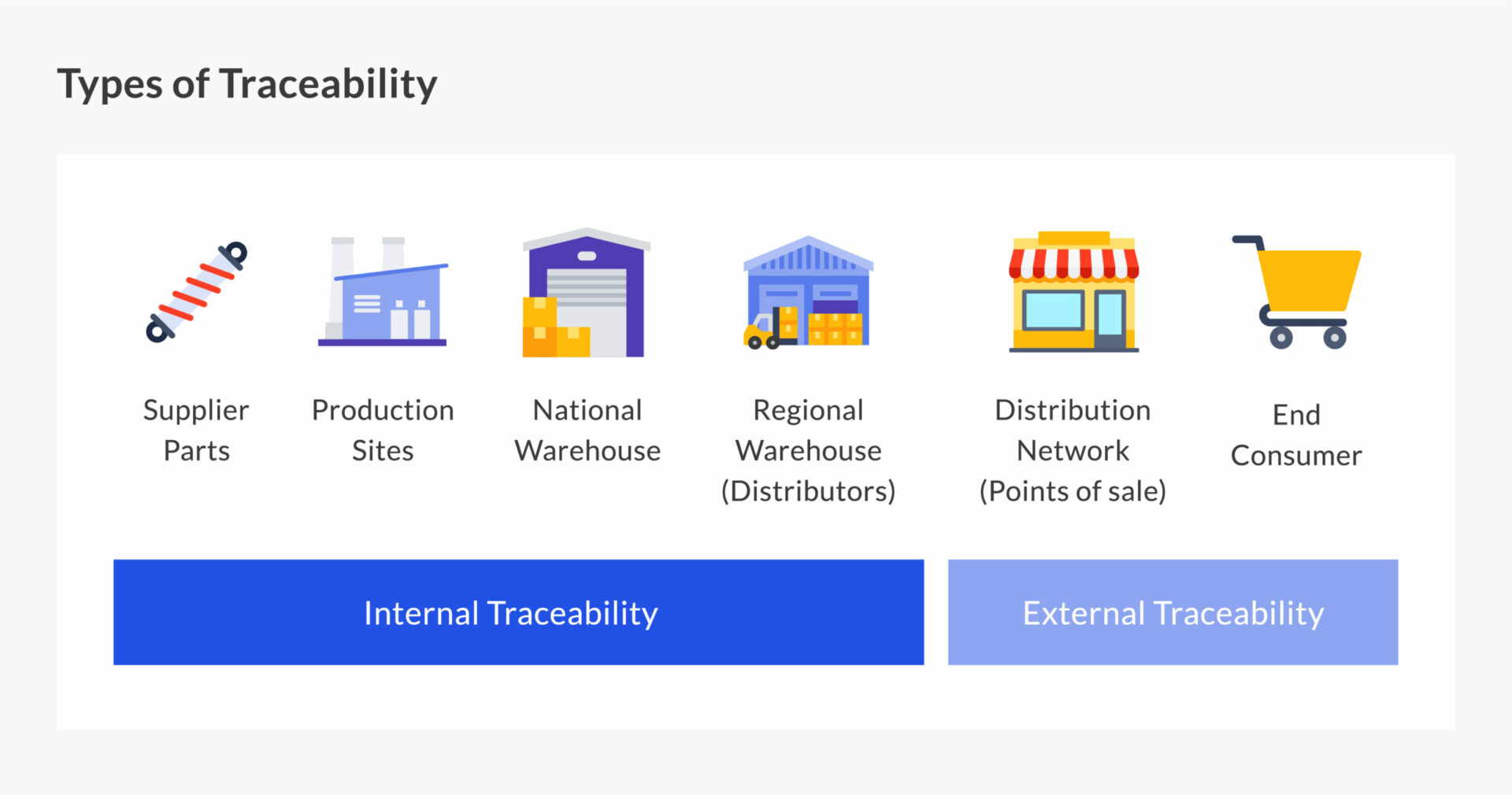
- Internal traceability: This covers all aspects of track and trace during the production process and is typically within the confines of the factory floor. Internal traceability is particularly relevant for large factories with several plants spread across locally or outside the borders of a country. It provides specific details on the exact company plant and production sector where a product is being/ has been created.
- External traceability: This is the ability to trace where the raw materials of the products were sourced and to chart the course of the product’s journey after leaving the factory. External traceability can be consistent with the direction of the supply chain i.e., enabling product trace downstream from raw materials via manufacturing all through to consumer or in reverse of the supply chain i.e., enabling product trace from the consumer back to the factory and even the raw materials.
Four all-encompassing reasons why your manufacturing company needs a track a trace solution
- Guides better management of product recalls
- Planning and forecasting
- Maximizes ROI
- Enhances customer satisfaction
Guides better management of product recalls
Traceability enables factories to minimize the broad effect of product recalls when safety issues or product defects are discovered. With a track and trace system in place, manufacturers can know exactly when standardized processes deviate from the norm and at what stage of the production process a defective part (or unsafe ingredient) was first introduced.
This knowledge empowers the factory to quickly identify the source of product problems, pinpoint the lots or batches at risk, and make informed decisions on how to manage the defective products at large. Subsequently, the factory can contact retailers to swiftly remove the product from shelves. This will reduce the risk of costly litigations and limit the exposure of customers to potentially dangerous products. Afterward, the factory can then proceed to tracing the products to the customers and/or issuing general product recalls.
Planning and forecasting
Traceability provides a real-time ‘location view’ of raw materials, assemblage, and finished products thereby enhancing visibility across the supply chain. At the pre-production phase, this information enables manufacturers to better manage their inventory, and juggle the different pieces to accommodate and complete orders in a timely manner.
Post-production, supply chain data (culled from the track and trace system) can be aggregated in a digital solution to provide insight into patterns and emerging market trends. Factories can use this information to gain a competitive advantage and manage resource optimization, even as they unlock new revenue streams and opportunities.
Maximizes ROI
Without the ability to troubleshoot quality issues quickly and effectively, factories are susceptible to more costly interventions and ensuing downtime (partial or total), pending the resolution of the issues. Even more, in the process of ‘blind resolutions’, factories may resort to calculated guesses that affect more products than necessary leading to waste and inefficiencies. But sometimes, these issues may not be easily discernable i.e., interaction between several chemical components in production transit.
A track and trace system enhances the capability of factories enabling them to thoroughly scrutinize each phase of the production process and accurately deduce the fault points. Empowered with this knowledge, they can pinpoint the product(s) at risk using individualized serial numbers or batch numbers – minimizing waste and fostering agile manufacturing in their plants.
Enhances customer satisfaction
Traceability positions factories as the proverbial master of their destiny, giving them more bandwidth to serve customers with products of the best quality. Manufacturers can source high-quality raw materials, without worrying about in-transit counterfeiting. Also, they can measure to a higher degree of certainty the product constituents – including additions at each stage of the process – helping them to more closely align their products with quality standards. And if for any reason the products fall foul of these standards, the factory can quickly issue recalls and protect the customers from defective or otherwise dangerous products.
These abilities in addition to the factory’s ability to better manage inventory will improve the quality and timeliness of the final products that arrive at the doorsteps of the customers. Furthermore, downstream traceability allows manufacturers to conduct more personalized marketing campaigns and show customers that they’re not just statistics, but matter as individuals to the factory.
On the part of the customers, the ability to trace the product genealogy upstream will breed trust, and when utilized, increase their confidence in the product.
Why Maximl?
Maximl helps factories manage the process of implementing a track and trace solution. Our platform easily integrates with 2D barcodes and other ‘product identifiers’ to provide a real-time measure of product quality within the factory and analyze tracking data inside and outside the factory. We have the scalability to grow with your factory and resiliently store supply chain data for future analysis.
- Easily accessible and can resiliently store tracking data
- Solve time-sensitive problems quickly
- Helps to quantitatively measure product quality
- Works operationally in real-time – automatically documenting a product’s journey to ensure that no step is skipped for quality compliance.