In a multi-faceted industry like manufacturing, it’s foreseeable that problems will develop at some point during the production process. The outcome of the problems – derailed production or process-improvement – will depend on whether they’re ignored or solved; left exclusively for the management or taken up by individual workers. In this article, we examine how you can standardize problem-solving in your factory and bring out the problem-solver in each one of your workers.
The American Society for Quality defines problem-solving as ‘the act of defining a problem; determining the cause of the problem; identifying, prioritizing, and selecting alternatives for a solution; and implementing a solution.’
All factories generally start out to solve problems; the challenge is to continue solving problems. The greater the factory scales, the greater the problems it will encounter. Shying away from problem-solving will only shrink growth and stabilize mediocrity.
This is applicable to stakeholders on a shop floor. Manufacturing workers may not be able to stop problems from developing, but they can – with help from the management – improve the quality of their response to these problems. They can act just as prudently as managers would and resolve problems before it progresses to something more serious. When such a culture of problem-solving becomes a factory’s normal, managers will be able to channel their time and creative energies towards growth.
Four steps to create a problem-solving culture in your factory:
- Cultivate a problem-solving attitude
- Develop workers in line with a problem-solving framework
- Create a platform to conveniently report problems and brainstorm solutions.
- Refine, rework, and normalize solutions.
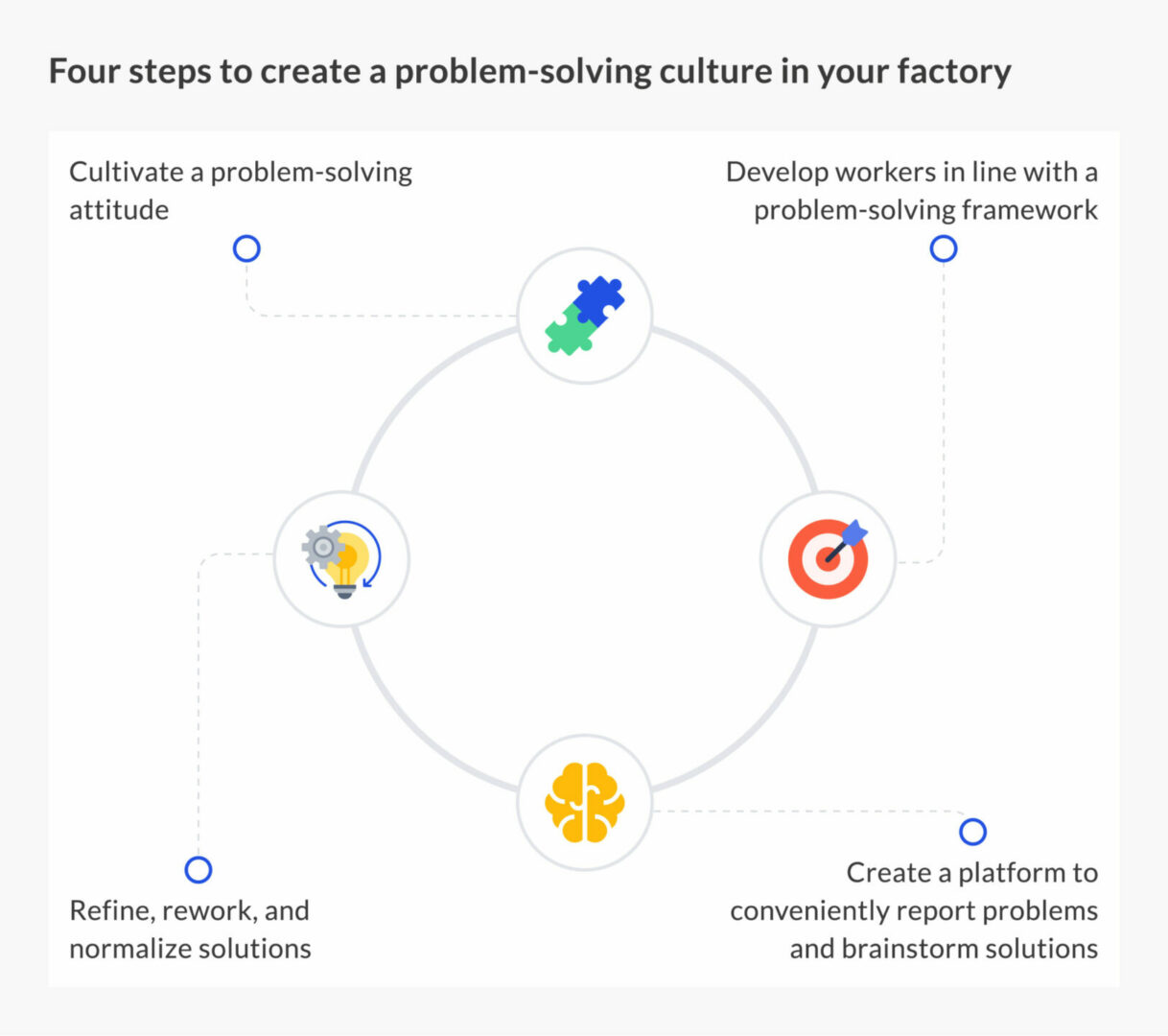
1. Cultivate a problem-solving attitude
If the attitude of your workers is to ignore problems, and the workplace environment is one that stifles creativity, or dishes retribution for thinking outside the box, problem-solving will be absent. Instead, workers will turn a blind eye to problems and actively encourage others to do so.
To make problem-solving the standard pattern in your factory, you first need to cultivate a problem-solving attitude. Right from the top of the organogram, everyone should be taught to see problems as opportunities for growth. It should be clearly stated in on-boarding and training programs that the minimum expectation for workers is problem ownership. And this should be evident in the positive attitude of the management – devoid of ‘blaming’ and ‘shaming’.
The problems may be varied and outside the scope of what workers can handle, but at the very least, they should report any anomalies they notice during the course of their jobs.
2. Develop your workers in line with a problem-solving framework
While you want to encourage workers to take initiatives and offer solutions for problems, there must also be the recognition that they can only solve problems within the confines of their skill-set. As such, personal development and tailored training should be made available for your workers.
Depending on your problem-solving framework, workers may need to (re)learn important skills like critical analysis, quantitative analysis, creative thinking, fishbone diagrammatic analysis, and how to use relevant software tools. They will also need a deeper understanding of the problems that may arise during the course of their jobs and how to identify root-causes.
Organizing training and programs for workers, consistent with a pre-established problem-solving framework will help your workers tackle issues better and more efficiently.
3. Create a platform to conveniently report problems and brainstorm solutions
Sometimes, problems are not reported simply because workers lack appropriate channels for reporting and laying bare the severity of the issues. Even when they manage to report the problems, lack of effective collaboration tools leaves everyone working in silo – hindering the process of problem-solving.
Maximl eliminates this problem by simplifying the process of problem-reporting.
On our Connected Worker platform, workers can easily report problems – and upload multimedia information with comments, images, and videos. Stakeholders, far and wide, can then view the reported problems to collaborate around clarification, a root-cause, and an action plan for resolution.
Even more collaboration can strengthen virtual team meetings, where pending problems may be assigned to a specific group of workers for resolution. The digitized materials, books, and standards available on the platform will smoothen the process of problem-solving. As will video calls, with which workers can access expert guidance and reduce the mean-time to resolution.
4. Refine, rework, and normalize solutions
Now that you’re likely faced with several suggested solutions to a problem, the next step is to see how these solutions hold up in real life.
Some factories fall foul of the ‘rushing syndrome’ where solutions that look good on paper are swiftly implemented without careful thought or digital-backed deliberations. Eventually, these solutions may prove insufficient, and extra resources will have to be devoted to implementing a new solution.
Maximl allows you to:
- Project the feasibility of suggested solutions with virtual ‘testing’
- Model their impact upon implementation
- Contrast the effect of all solutions
- Ensure design specifications are met with digital calculations.
- Standardize field operations with visually rich and easy to understand SOPs
We also enable you to digitize the solutions and embed them into your manuals, procedures, and day-to-day process.
Besides, after implementation, you can use our quantitative analysis tool to measure the impact of the solution on your performance metrics and ascertain whether or not it still solves the problem for which it was intended.